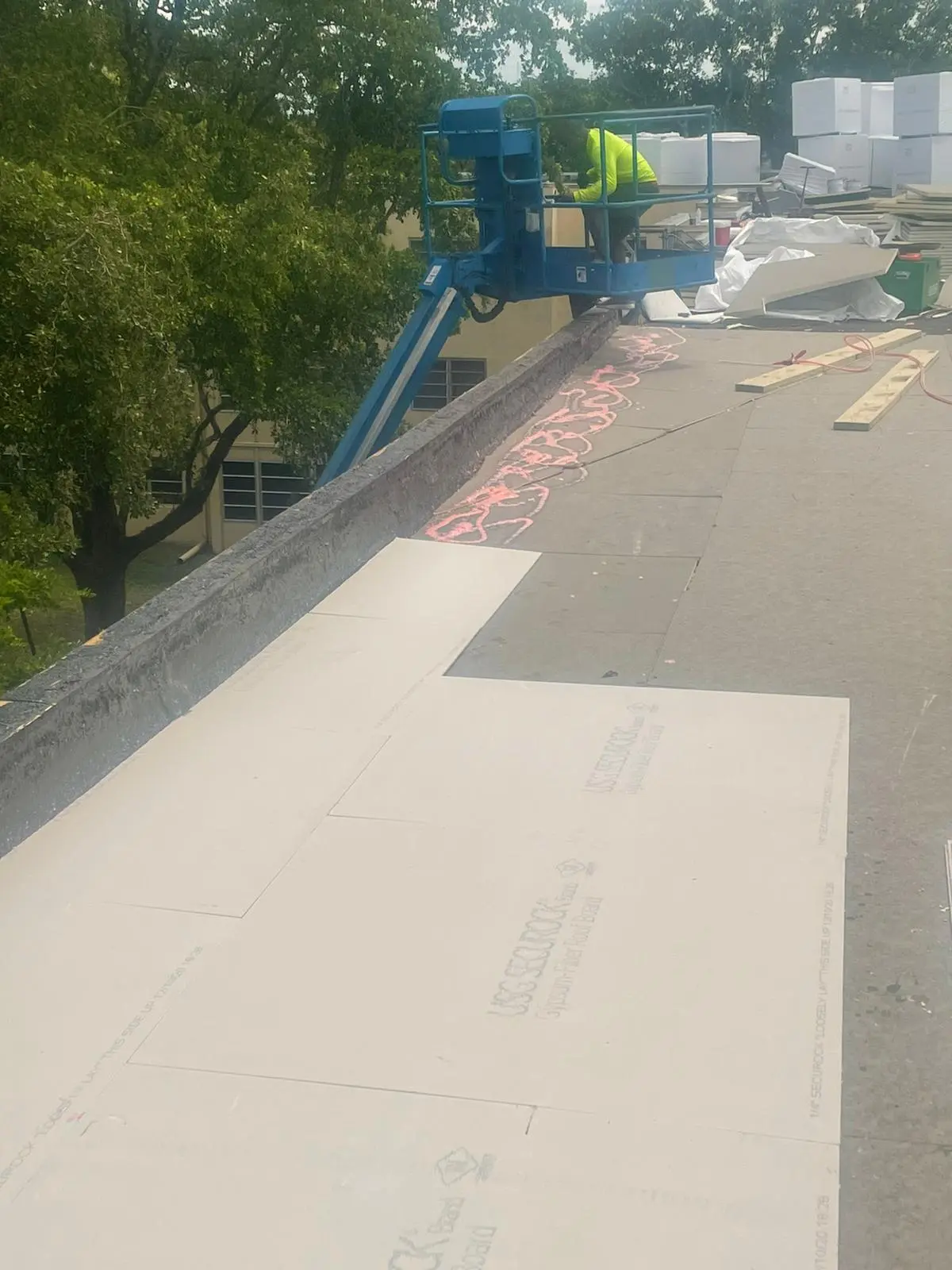
Industrial Roofing Systems In Florida
Differences Between Commercial and Industrial Roofing
Although the terms “commercial roofing” and “industrial roofing” are often used interchangeably, there are notable differences. Generally, industrial roofing is viewed as a segment of the overall commercial roofing industry. Commercial properties involve the business or professional use of a non-residential structure or building. They typically encompass everything from restaurants and retail shops to warehouses and factories. Industrial properties have a much more limited scope. They usually incorporate factories, power plants, warehouses, and shipping centers.
StormForce Roofing works with industrial property owners and building managers to provide exceptional roofing services. We understand the unique challenges that come with servicing industrial roofing. Whether your structure requires roof repair, maintenance, or replacement, we offer expert guidance, unmatched craftsmanship, and the highest quality roofing materials to ensure long-lasting roofing solutions. Industrial property owners and building managers trust us to deliver prompt, professional, and budget-conscious roofing services without exception.
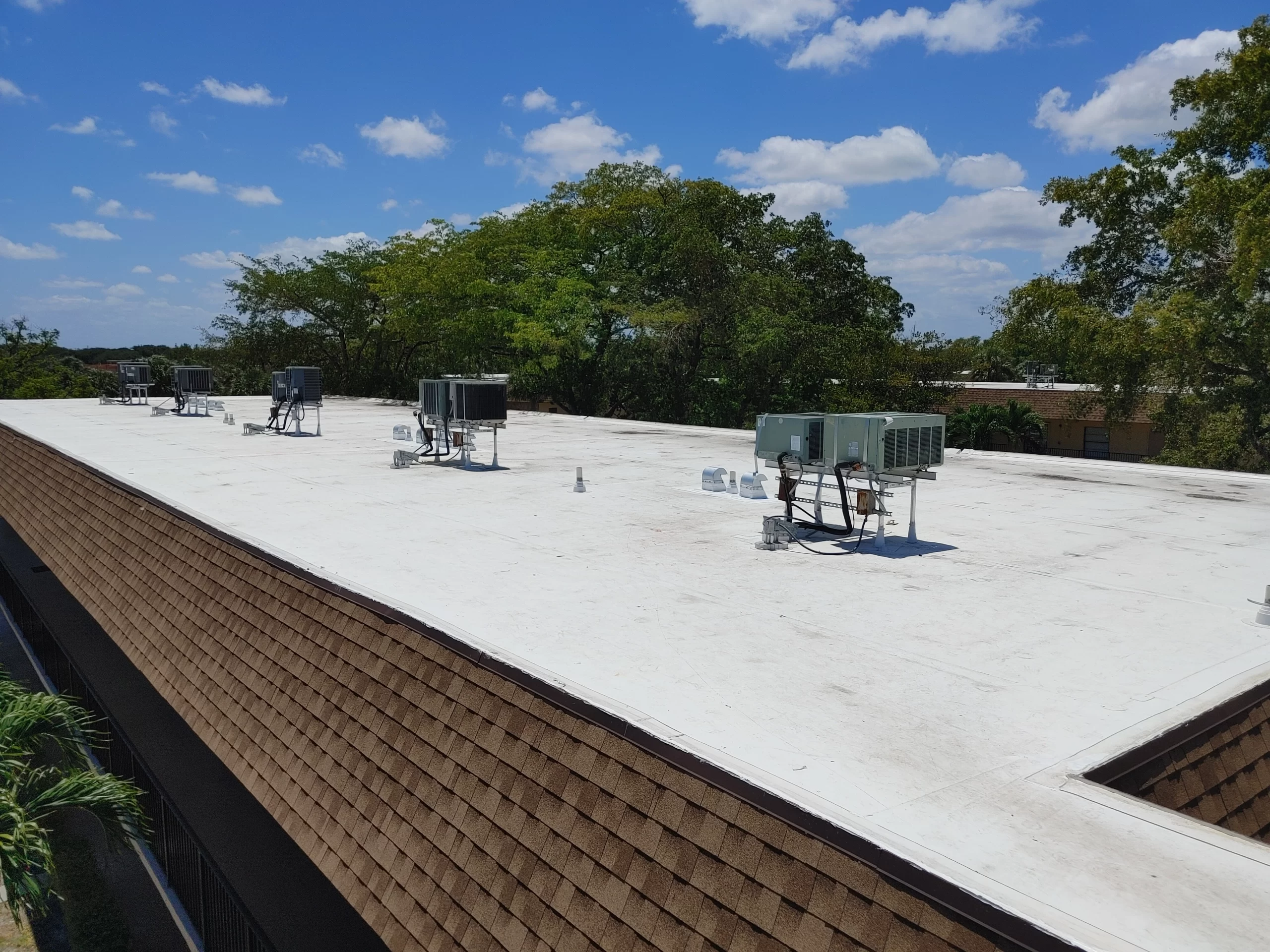
Defining An Industrial Facility
Like any real estate classification system, industrial facilities encompass a variety of buildings and structures designed to promote functionality over aesthetics. Typically, industrial complexes are intended to support heavy machinery and equipment. Often, they will utilize an open floor plan with high ceilings (and, in many cases, incorporate an extensive amount of natural light.)
Because industrial facilities are subject to strict regulatory guidelines, compliance issues (from local, state, and federal governments and agencies) can be complex and difficult to understand. How a roof is constructed, managed, and repaired significantly contributes to this regulatory equation. Thus, you should only work with a highly experienced industrial roofing contractor.
Industrial buildings usually fall into one of three primary categories:
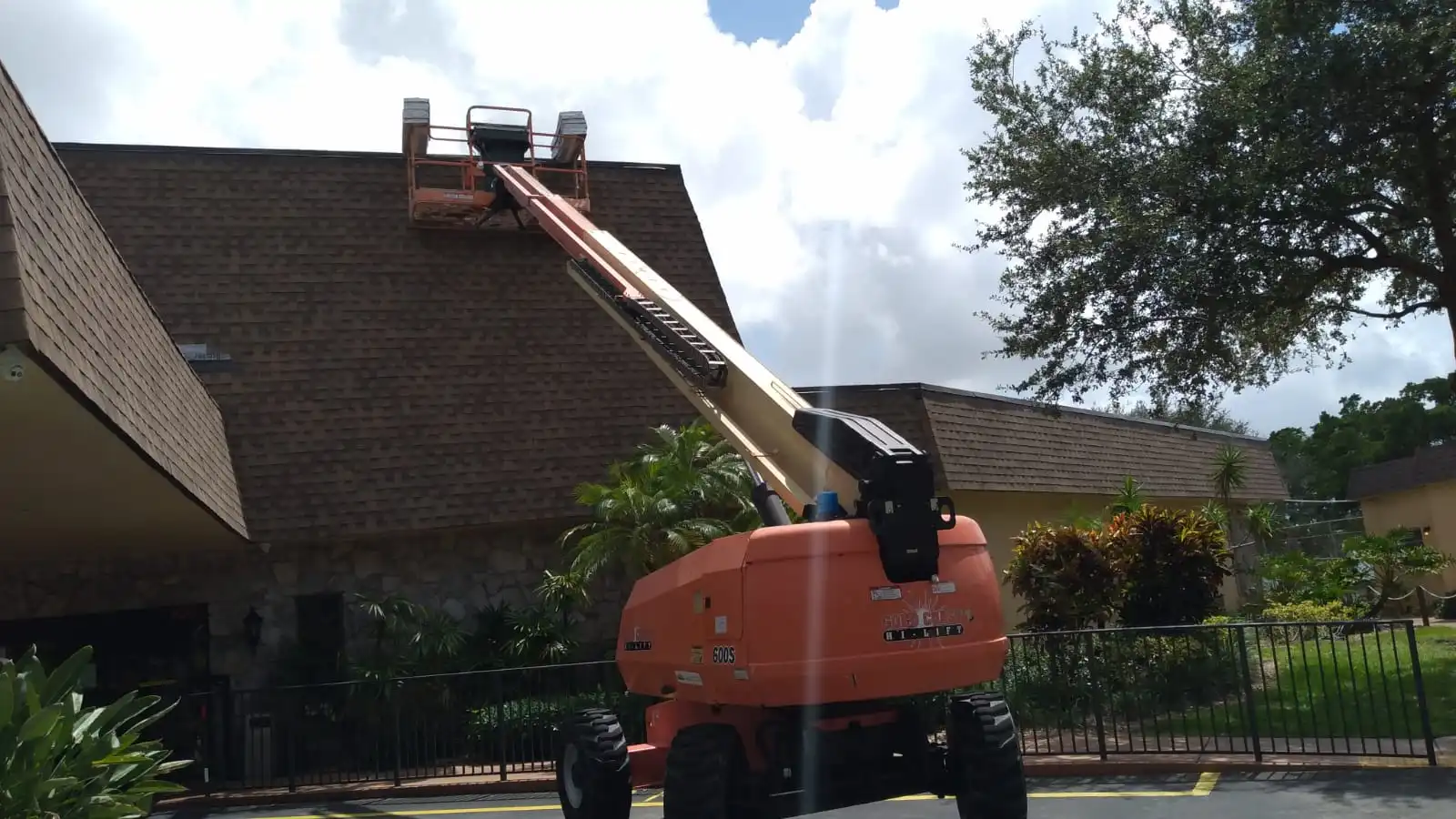
Roof Repairs For Industrial Properties
Commonly, industrial facilities involve an expansive layout with thousands (if not tens or hundreds of thousands) of square feet of roofing. With such a large building (or buildings) to monitor, industrial property owners and managers often have difficulty identifying problematic areas (or spotting potential issues that may require addressing in the very near future.) In fact, some roofing challenges can take weeks or even months to notice.
In addition to outside or natural elements (such as rain, wind, hail, snow, or ice), manmade chemicals, exhausts, and residues from various manufacturing processes often will adversely affect the composition of roofing materials (and the building’s structural integrity.) The impact of these forces produces premature degradation or erosion of an industrial building’s roofing system. Restoring the roof becomes necessary before it’s too late.
Comprehensive Industrial Roofing Solutions
At StormForce Roofing, we address the following roofing problems with common-sense, long-lasting solutions:
- Billowing Roof Materials
- Breaks and Shrinkage
- Broken Seams
- Hail Damage
- Ponding Water
- Punctures, Holes, and Tears
- Reinforcing Weak Points
- Replacing Flashings
- Ridging and Splitting
- Roof Leaks
- Securing Loose Tiles/Shingles
- Storm Damage
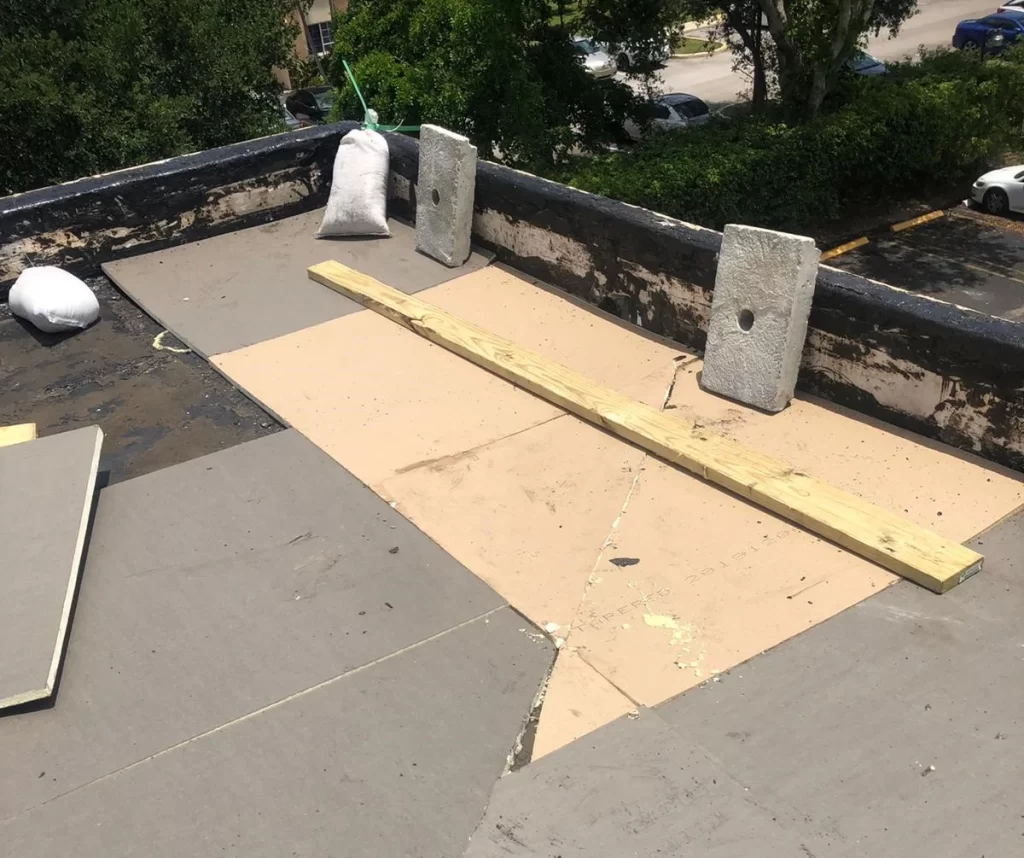
Industrial Roof Replacement Services
Typically, a roof replacement is a significant undertaking (in terms of time and expense) because of the relative largeness of most industrial facilities. Deciding to remove and replace an existing industrial roof with a new one requires careful consideration and conscientious budget planning. A business may also experience a certain amount of operational disruption (i.e., downtime) and involve a significant adjustment of logistical considerations (at least temporarily.)
Knowing what type of industrial roof best serves your needs demands a thorough understanding of many relevant factors. For example, you should analyze what kind of ventilation system your building incorporates. Your geographical location and prevailing weather conditions play a significant role in determining your ideal roofing system. For example, if you want to maximize natural lighting entering your building, you will want to consider whether skylights make sense.
Many kinds of industrial roofing systems exist depending on your needs and preferences. They include the following options as outlined below:
Type of Industrial Roofing Material | Features & Benefits |
Asphalt Shingle Roof |
|
Built-Up Roof (BUR) |
|
Concrete Roof |
|
Ethylene Propylene Diene Terpolymer (EPDM) Single-Ply Roof Membrane (Thermoset) |
|
Green Roof |
|
Metal Roof (Corrugated or Galvanized) |
|
Modified Bitumen Roof |
|
Polyvinyl Chloride (PVC) Roof (Thermoplastic) |
|
Roof Coating Systems |
|
Spray Polyurethane Foam (SPF) Roof |
|
Thermoplastic Polyolefin (TPO) Single-Ply Roof Membrane |
|
Tile Roof |
|
Contact StormForce Roofing today to schedule a complimentary consultation and receive a free inspection to assess your industrial roof’s condition.